
Meggitt High Temperature Materials
In addition to my senior thesis in physics, I petitioned to be part of the Engineering Clinic program at Harvey Mudd, a program that allows students to work for private sector companies under the guidance of a faculty mentor. As a member of the five-person Meggitt High Temperature Materials team, I worked on the multiple issues related to exposing sensor and valve components to temperatures up to 400°C. The end goal of this project is to allow Meggitt’s products to operate closer to the center of jet engines. This would allow for the reduction of engine cross-sectional area, thereby decreasing both drag and weight. My team was tasked with finding solutions to two main issues, and two stretch goals. In the 2019-2020 school year, we researched materials, conducted thermal testing, and designed further vibration testing through NTS, all the while coordinating with our liaisons at Meggitt in weekly teleconferences and participating in design reviews with the Toyota, Niagara Bottling, and Sandia National Labs clinic teams. We officially presented our progress to the entire Engineering Clinic program at the start of the Spring Semester, and to our project partners in mid-year and end-of-year presentations.
Problem Descriptions
Main Issues
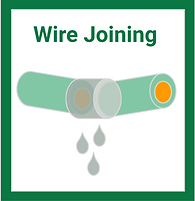
Soldering is the method of choice for most electrical connections. Common electrical solders melt between 180 ºC to 190 ºC. The team developed and tested electrical component joining alternatives that can withstand high temperature environments up to 400 ºC. Though the joints will not be under tension inside Meggitt's components, the team conducted tension tests to validate the quality of the potential joints. The team developed a test fixture in order to conduct vibration tests at the National Testing Services to see if the joints would comply with MIL-STD-810H vibration standards. Unfortunately, due to quarantine and the halting of all technical work, these tests have yet to be run. However, CAD drafts have been provided to Meggitt, allowing them to machine the fixture and run the vibration tests in the future.

The nickel-coated copper wires used in the primary magnet coil of the LVDT are 38 AWG (0.0040” or 0.1 mm in diameter). Wires with a diameter of 0.15 mm or less exhibit rapid and permanent changes in resistance when exposed to high temperatures, due to interdiffusion of the nickel and copper. This interdiffusion creates an alloy zone at the interface of the two materials, which has a higher resistance than either nickel or copper individually. As the primary coil is meant to supply an alternating magnetic field of unchanging magnitude, a change in resistance over time can result in the LVDT providing inaccurate position measurements. The team researched and tested wire alternatives that maintain a constant level of electrical resistivity in environments of temperatures up to 400 ºC over an indefinite period of time.
Stretch Goals

Current aerospace insulation options such as PTFE can withstand temperatures up to 400 ºC; however, the color-coded insulation materials used by Meggitt fade into the same color when exposed to operating temperatures of 400 ºC. Other commercially available insulation materials that do not change color when exposed to high temperatures do not come in a variety of colors. Meggitt desires the ability to easily differentiate between the lead out wires connected to the LVDT of Meggitt’s engines before and after exposure to high temperatures. The team investigated and tested alternatives for wire identification that can withstand aerospace environment temperatures for an indefinite period of time.
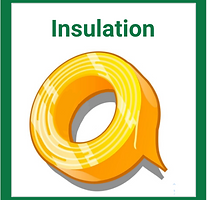
Because of its light weight, thin profile, low electrical conductivity, and high dielectric strength, Kapton film has been a standard insulation material for the aerospace industry. At temperatures above 260 ºC, the properties of Kapton film deteriorate. The team researched insulation alternatives that meet aerospace standards for temperatures as high as 400 ºC.